latest
Why we are optimistic about the state of manufacturing in the UK

The ominous headlines about UK manufacturing over the last few weeks have focused on the challenges of supply chains, labour shortages and an uncertain economic environment. In recent days, however, more upbeat assessments such as the latest CBI Industrial Trends Survey comment that “in January 2023, more manufacturers thought that output would rise over the next three months than thought it would fall”, reflects our experience at Chetwoods far more accurately.
Our position as architects who are extremely active in the industrial and logistics sector, with over thirty years’ experience, gives us a good understanding of general pipeline and insights into trends a couple of years ahead. Our conclusions are supported by our own research projects into the Industrial Intensification sector, supported by the market insights of our project teams and CEO Tim Ward who is a member of New London Architecture’s Industrial and Logistics Expert Panel.
We are experiencing increasing manufacturing demand
We also have the evidence of live projects where we are currently working on over a million square feet of manufacturing space in England. What is interesting is the manufacturing sectors that these projects are in. The media stories have reflected undoubted problems in sectors such as car manufacturing, whereas at Chetwoods we are seeing an increase in UK operators who are expanding their manufacturing in response to the UK’s sustainability ambitions and to support the housebuilding sector’s agenda to build more homes.
These include companies that are manufacturing construction materials some expanding where the workforce is; some expanding to meet demand whilst reducing transport logistics costs. One client is developing a new site in addition to its existing sites in the UK, another is looking to scale-up manufacturing in the UK to reduce the cost and environmental impacts of importing its products.
Locating and developing manufacturing sites poses very different challenges from pure logistics which can be built speculatively. The key requirement of manufacturing is the recruitment and retention of skilled labour. Whereas logistics sites have a regional ‘hub’ focus, manufacturing thinks in terms of a radius of just a few miles to access local skilled labour.
Land supply is constraining manufacturers’ ambition
We are seeing that the constraints for some of the UK manufacturers we are working with is not lack of demand holding back their ambition but the problem of the right land supply in the right locations. They are searching for available sites that will enable retention of the existing workforce – with the vitally important local transport and infrastructure plans needed to support any relocation – or sites elsewhere in the country to support increasing regional demand for their products which are near a new skilled workforce. This is a point of differentiation when compared to our logistics developments
Manufacturing construction on-site
We are currently on site with a scaled-up manufacturing and distribution site for TopHat, a company at the forefront of the UK’s modular house-building revolution. The development builds on the success of TopHat’s existing site in Derby which already produces up to 800 homes per year. At nearly seven times the size of the company’s existing site, the new 650,000 sq ft facility (equivalent to 11 football pitches) at leading global logistics development manager GLP’s new Magna Park in Corby, Northants will be Europe’s largest modular homes plant which is expected to be delivering its first homes by the end of 2023.
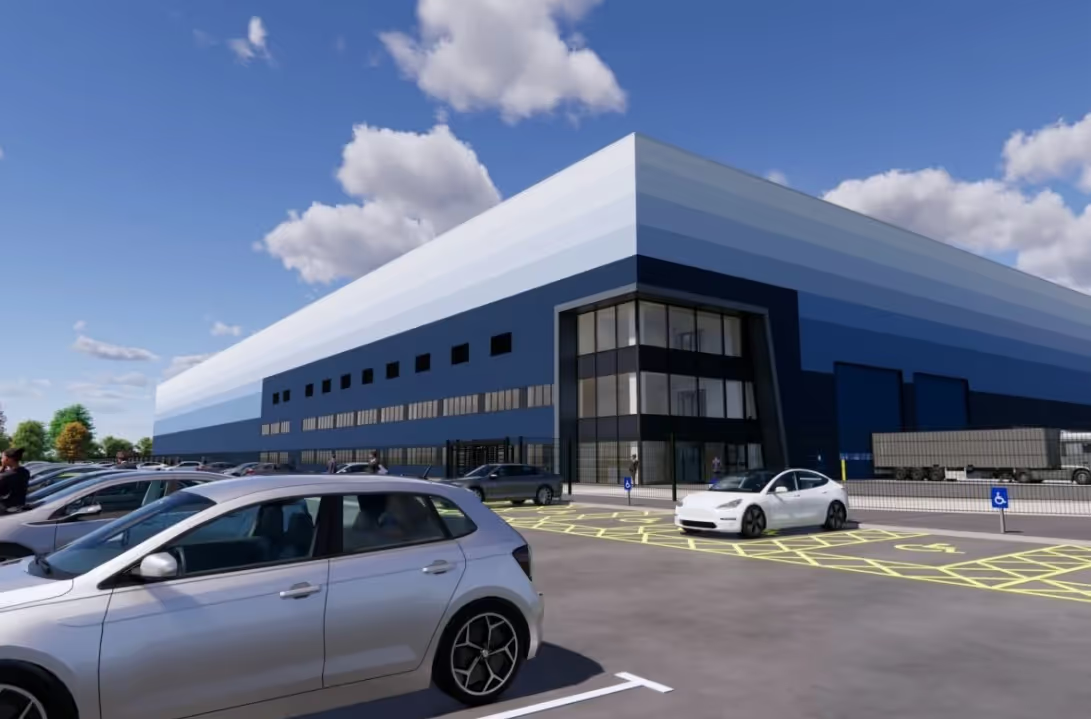
As with our logistics developments, there is an on-going push to reduce carbon emissions and improved sustainability targets in construction by responsible material specification, waste reduction through efficient design and supply chain and sourcing considerations. There is also a similar push for the building in operation, led by developers, funds and occupiers to ensure they adhere to their renewed ESG policies and sustainability goals. As we have previously noted in projects such as our redevelopment of Didcot Quarter to repurpose a brownfield site into a high-spec industrial complex designed with employee health and wellbeing at its heart, ESG — environmental, social and governance — issues have become more of a concern for manufacturers.
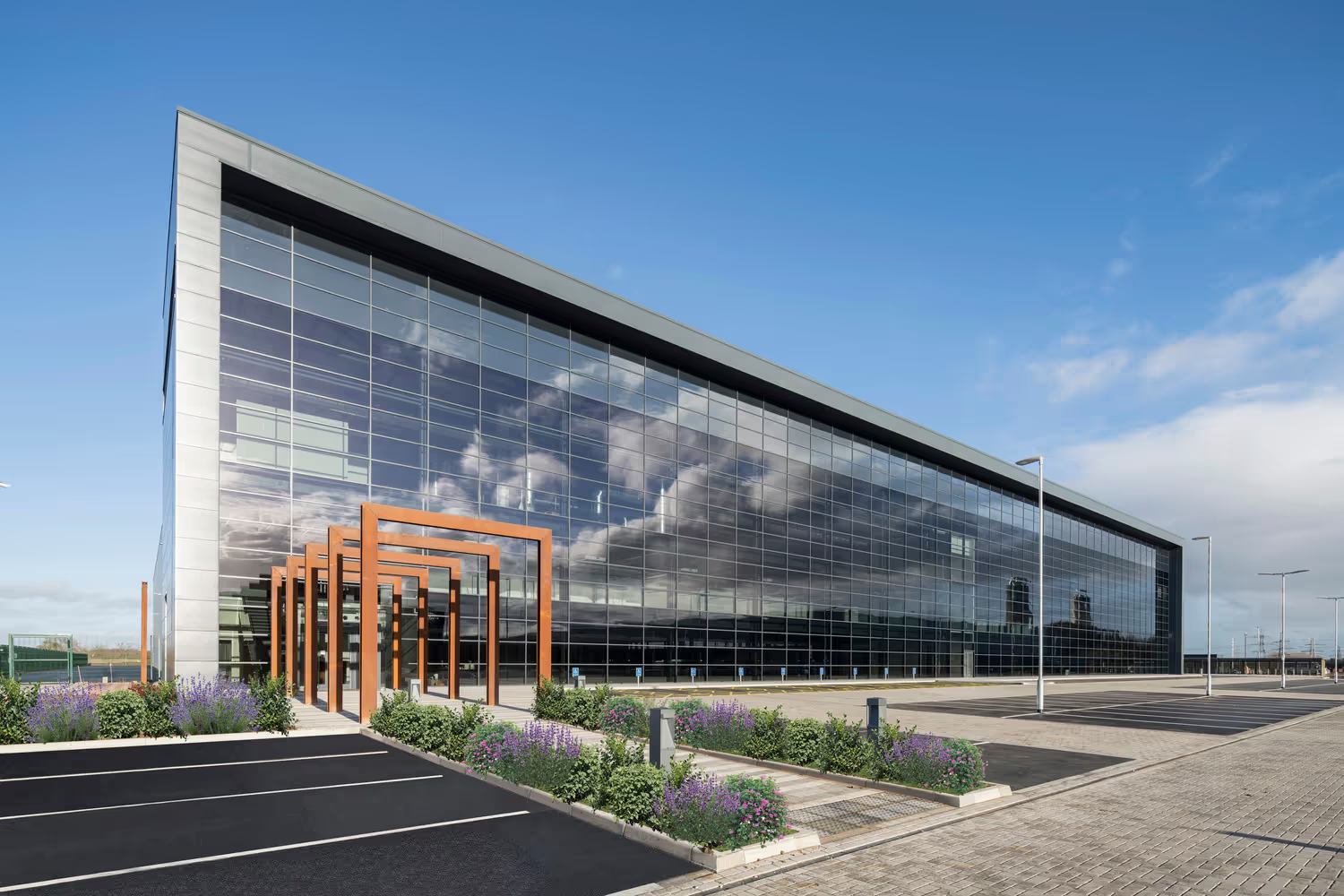
Sustainable processes and the adoption of carbon-neutral practices across their businesses are increasingly enshrined from the beginning of the design and construction process, as are new ways of monitoring and maintaining employee health to standards formerly associated with commercial office workspaces.
Manufacturers are also looking at the technologies that can be built in from the start to help them manage efficiency and maintenance costs-in-use to increase efficiency and support the wellbeing of their valuable workforce.
Conclusion
In conclusion, our own experience and current design and construction pipeline in the manufacturing sector is encouraging, with grounds for optimism, in particular with regard to operators who are actively expanding their manufacturing in response to the UK’s sustainability ambitions and to support demand from the housebuilding sector. We are also seeing encouraging progress in companies wanting to literally build technology and sustainability into their buildings to support their commercial, social and environmental ambitions.
Article tags
Share this insight